OUR STRENGTHS
- Compactness
- Simple operation
- Traceability
Thanks to our experience in impregnation and process automation, we can design and manufacture complete impregnation machines for all your specific needs. Our machines allow:
- to link components/layers
- leak tightness
- the alteration of properties
Vacuum or pressurised impregnations meet the requirements of components that have high technical specifications.
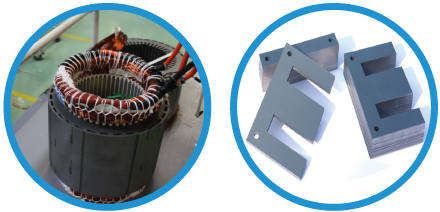
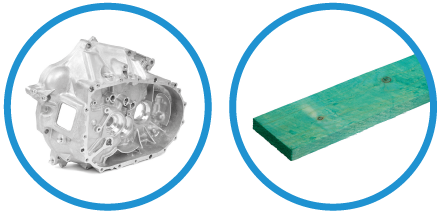
Transformers, electric motors and alternators are composed of copper wire coils (or plates) and cores formed of a stack of thin magnetic plates. These elements are permanently subjected to magnetic fields, differential dilations, centrifuge forces, as well as mechanical vibrations. All these stresses generate micro-movements that can damage insulation and create short circuits in the long term. This causes local overheating, serious malfunctions or even the complete destruction of the equipment. Impregnation is used to inject a suitable resin or varnish to the core to strengthen component insulation and hold them together.
Effective impregnation requires a strong vacuum in order to remove the air trapped in the voids and replace it with resin without trapping any air bubbles. An optional pressure cycle allows for deeper resin penetration if necessary. Better thermal exchanges in the conductors and a significant reduction in local hot spots is then noted.
An impregnation installation is composed of one or more resin tanks, a vacuum impregnation autoclave, a vacuum pump and a resin purifying filter. The equipment can be in a single block with the autoclave placed over the tank, or with a separate tank. Depending on the layout configurations, the varnish is transferred using pressure difference, gravity or a pump.
Main options:
- Impregnation cycle automation and traceability
- Vertical or horizontal autoclave
- Doors on hinges or an arm with manual or automatic opening
- Storage tank under vacuum
- Handling of products to be impregnated (trolley, false tanks)
- Tank heating or cooling using a heat insulated double wall
- Heat exchanger to bring the resin to temperature when transferring it to the autoclave
- Mixer/stirrer on the tank used to churn the varnish to maintain consistency and temperature
- Autoclave heating with a double heat insulated wall and a thermal oil warmer
- Strengthened filtering (200µm) on the line that transfers the varnish to the autoclave
- Condenser before the vacuum pump with cooling unit to protect for varnish vapours
- Stronger vacuum using a multi-stage pump system
We propose automatic, high speed machines for the impregnation of cast aluminium parts for the automotive industry. They are fitted with a handling arm, a centrifuge spin-drying system, rinsing and firing tanks and a water and resin separator to optimise product consumption.
We can therefore meet all your impregnation needs, regardless of the material to impregnate and the fluid used, subject to a compatible vapour tension curve. Research is currently being conducted in partnership with researchers to develop a wood variety impregnation process.
Main options:
- Robotised handling arms for high speed operation
- Upstream part drying (atmospheric or vacuum)
- Spin-drying and /or rinsing
- Firing/polymerisation system
- Weighing system to monitor resin consumption
- Measurement of impregnation product density
- Multi-product impregnation management
- Separation to optimise impregnation product recycling
- Automatic cleaning at the end of the cycle
