OUR STRENGTHS
- Performances
- Customisation
- Effective after-sales
Motor and transformer electric coils must be dried, polymerised or burnt off during their production or repair phases. We design furnaces suitable for these operations, that are perfectly heat insulated to reduce energy consumption and guarantee a wall temperature lower than 50°C. There are 4 types of process in our standard furnace line:
- atmospheric drying (transformer and motor)
- vacuum drying (transformer and motor)
- polymerisation (motor)
- burn-off (motor)
Our design office can also cater to all your heated chamber needs for your other specific applications: drying furnaces with a rotating “spit”, capacitor drying and impregnation furnaces, vacuum dosing and filling and then drying chambers for radiological ducting, tunnel furnaces, etc.
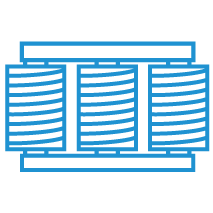
of a transformer
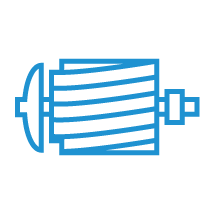
and polymerisation
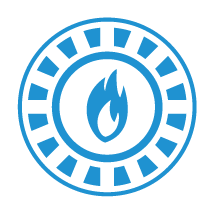
burn-off
Transformer coils contain many porous materials (wood, cardboard, etc.). Their drying is essential to proper transformer operation and increased service life.
Atmospheric drying furnaces heated to 200°C (300°C as an option) using hot air ventilation can be used to dry small transformers, electric motors or for other applications.
Vacuum furnaces, fitted with our self-adapting process, are recommended for the drying of the active part of medium and high power transformers. Compared to standard processes, drying times and energy consumption are optimised (2 to 3 times faster than a traditional atmospheric solution). Our vacuum drying processes are automated to optimise the alternating atmospheric and vacuum drying phases. Continuous temperature and moisture content (option) monitoring make it possible to minimise drying times.
Thanks to our processes, our furnaces achieve an exceptional level of efficiency for units of up to 120 tonnes. Compared to other more complex processes, they make it possible to achieve the same result for a significantly lower investment and running cost budget and avoid the use of any hazardous or polluting products.
Customisation:
- Bespoke production
- Door types (elliptical movement, side or vertical movement, cover on hinges with cylinders)
- Condenser to measure the amount of evaporated water
- Heating type (boiler or heat source provided by the client)
- Filling the transformer in a vacuum when drying is complete
- Built in coil calibration system during drying
- Handling rails mounted on a fold-away bridge at the entrance to the furnace
- Internal coil heating using low frequency current injection (LFH)
Hot air ventilated atmospheric furnaces are used to dry motors and polymerise resins and varnishes following impregnation without requiring the presence of operators.
Depending on product specifications, temperatures can be adjusted up to 200°C (300°C as an option). A programmer provides gradual heat rise for polymerisation furnaces. Compliance with the gelling and polymerisation steps eliminates thermal shocks and micro-cracking.
Customisation:
- Deferred start and programmer
- Recorder
- Trolleys
Our burn-off furnaces are mainly designed for the thermal decomposition of varnishes before unwinding a coil for maintenance operations (refurbishing electric motors). This operation is carried out at a temperature of between 300 and 400°C for 3 to 8 hours (depending on the type of insulation and the equipment size) in order to guarantee the perfect carbonisation of the varnish by pyrolysis. The resulting fumes then pass through a post-combustion box at 850°C to fully oxidise all pollutants before their release. Heating temperature regulation is provided by a self-adapting system that optimises the cycle time during the varnish degassing phases.
Customisation:
- bespoke production to client specifications
- Door types (two-leaf or sliding)
- Handling trolleys adapted to the handled element loads
- Rail track on the ground or embedded
